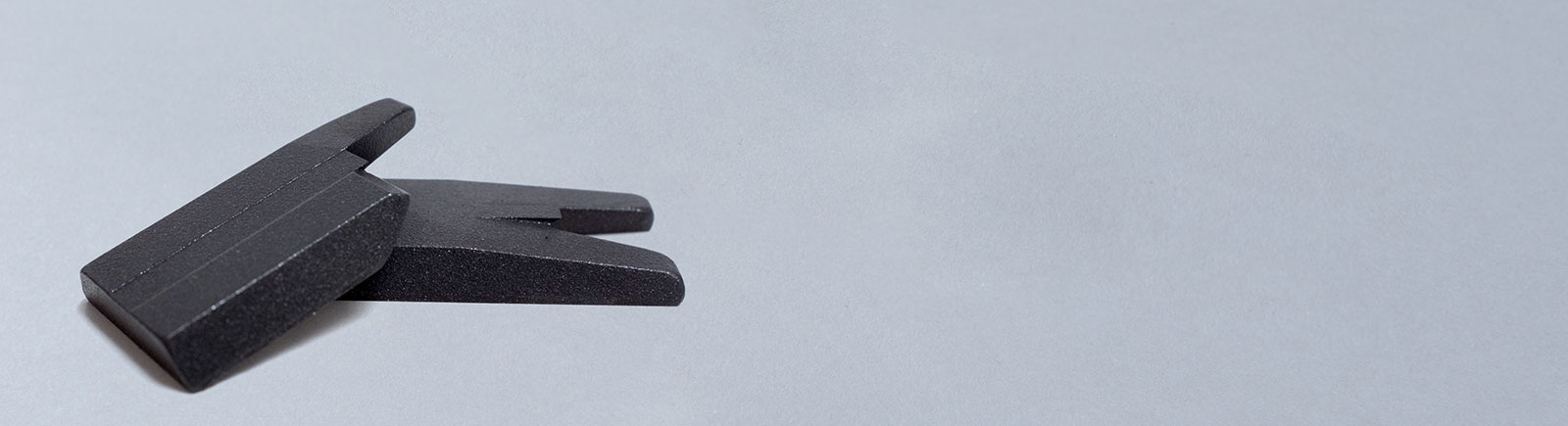
Prevent Costly Wear and Tear with Specialized Coatings from Adelhelm LubriCoat NA
Wear and abrasion resistant coatings
Equipment components wear down because contact between moving parts over time leads to abrasion and damage. It’s a universal challenge across industries. If this wear and tear isn’t treated proactively, machinery will reach the end of its life much more quickly, costing your business more than it should. Experts estimate two to four percent of industrialized countries‘ gross domestic product (GDP) is lost due to friction and the wearing out of mechanical parts.
Non-stick polymer coatings by Adelhelm LubriCoat NA gives machinery parts a low coefficient of friction, vastly reducing wear and abrasion of machinery components. FDA-compliant coatings are available to protect food/beverage and pharmaceutical production equipment. For the toughest challenges, Adelhelm LubriCoat NA can provide coating with the thermal spray system – the most durable non-stick coating available.
Get unrivalled protection with polyurethane coatings
In addition to wear resistance, coatings made of PU, PUR or TPU (polyurethanes) offer these benefits:
- Chemical resistance and corrosion protection
- Resistance to damage from impacts, cuts, tears and scratches – especially important for sensitive surfaces
- Flexibility and resilience – they distribute surface pressure to prevent uneven wear and high rebound elasticity (ability to absorb energy that could cause damage and bounce back)
Other available polyurethane coatings have special protective properties. Polyether polyols, for example, are resistant to low temperatures and microbes. Cross-linked polyurethane elastomer coatings are extremely tough, elastic, abrasion-resistant and have good damping properties. They can also include traction and friction modifiers to change the coefficient of friction and increase or decrease slippage or traction to suit specific applications such as those involving rolling components.
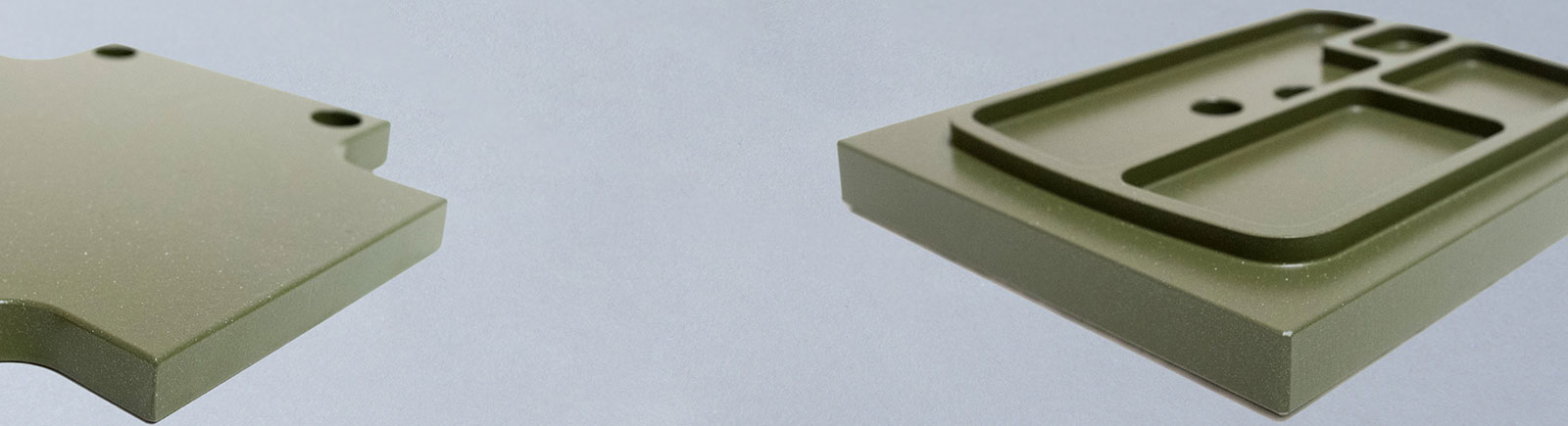
Thermal spraying for a range of options
Thermal spray (also referred to as metal spray) wear resistant coating protects new or used equipment parts with a layer tougher than the underlying material. Specific materials and processes, as well as coating thickness, should be customized to the part application, with the main consideration being stress profile (chemical stress, temperature, and related factors). The right choice also depends on specific wear concerns – abrasion, adhesion, fatigue, or reaction layer wear (tribochemical reaction).
Process and material options for thermal spraying include:
- Metallic and carbide materials (cored wires) can be cost-effectively coated by arc spraying
- For the most demanding wear situations, oxide ceramic materials such as chromium oxide can be applied by plasma spraying
(chromium oxide has a hardness of around 1500 HV0.3 and high chemical resistance over the entire pH range). - Highly wear-resistant carbide materials like WC-Co (tungsten carbide cobalt), with a hardness of around 1300 HV0.3, can be applied by high-speed flame spraying or plasma spraying
Combining thermal spray with polymeric topcoats such as PTFE (polytetrafluoroethylene) or PFA (perfluoroalkoxy) wear resistant coatings can be produced with a non-stick finish or other functional coatings.
Used
Brands
- Chemours
- PPG/Whitford
- Solvay
- Myline
- Arkema
Materials
Coated
- Steel
- Aluminum
- Cast Iron
- Stainless Steel
- Cast Aluminum